First flying in 1949, the de Havilland Comet was a breakthrough in the aviation industry, as it featured a series of revolutionary changes compared to the average aircraft of the time. Most notably, it was the first commercial airliner to feature jet engines. Featuring four de Havilland Ghost turbojets, the Comet 1 represented the future of the aviation industry, but at the same time created a major challenge for engineers. Much higher speeds and completely different aircraft performance characteristics forced engineers to venture into an area of aeronautics only tested on smaller military aircraft developed during World War II, such as the Gloster Meteor or de Havilland Vampire. Scaling up to the size of a commercial airliner would not be a smooth ride, as was discovered all too soon.
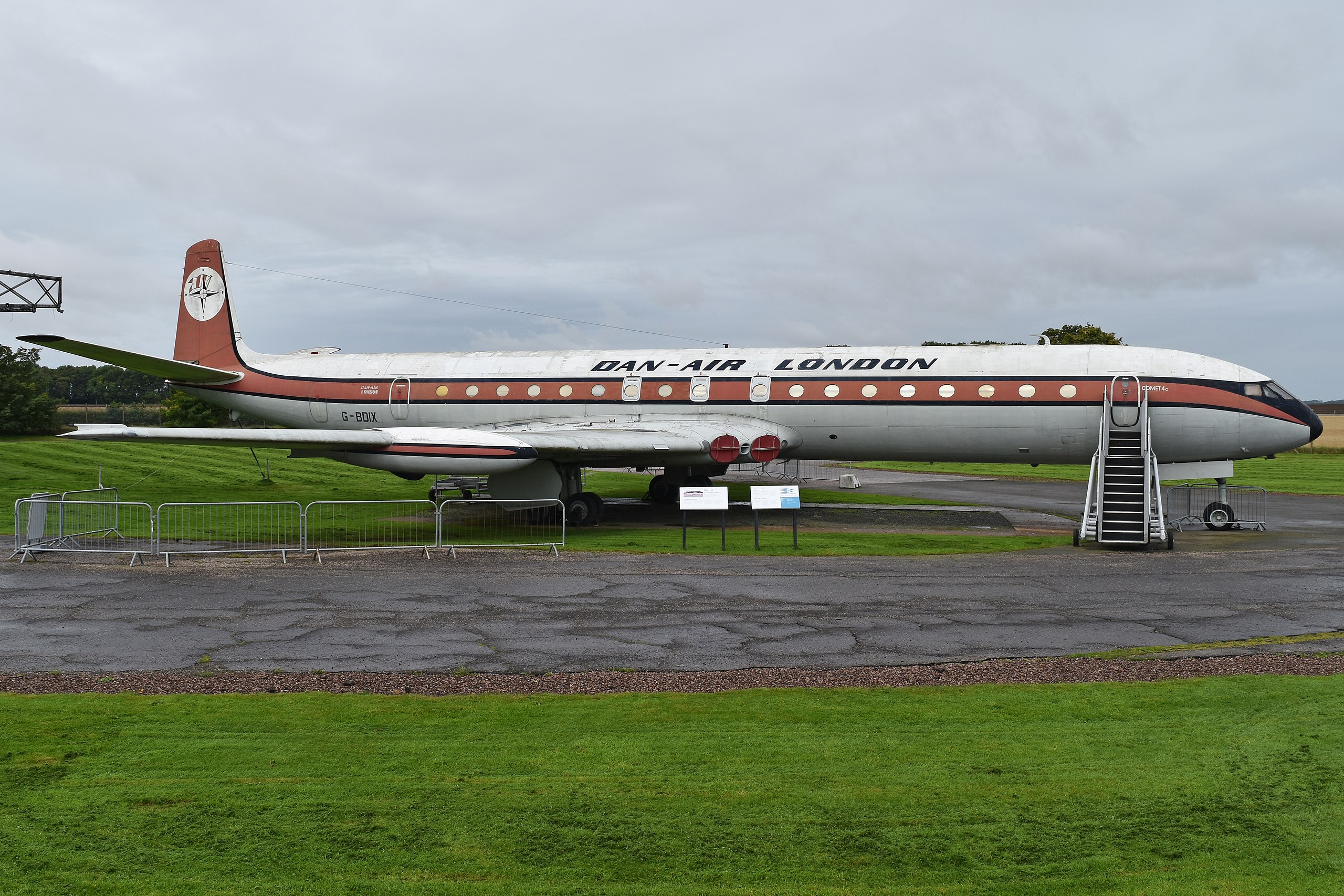
Critical Failures
The Comet entered commercial service with BOAC in May 1952, ferrying passengers between London and Johannesburg. Most notably, flight times were reported to be half of those on the most modern piston-engine aircraft of the time. However, the excitement for the new aircraft soon ended as the Comet suffered three major accidents in just 12 months. The first major accident occurred in October 1952, with a BOAC Comet did not get airborne at Rome-Ciampino airport, causing no casualties but severe damage to the aircraft, which was written off. While the cause of this accident was attributed to human error, two later crashes would forever damage the reputation of the Comet.
In January 1954, BOAC Flight 781 from Rome-Ciampino to London Airport (now London-Heathrow), operated by a Comet, was climbing through 27000 feet when it suffered a structural failure, crashing off the southern coast of the Italian island of Elba.
An investigation into the crash was started, which involved recovering the wreckage from the seabed. Once analyzed, experts concluded the failure had occurred in the fuselage of the aircraft, leading to an explosive decompression because of the pressure difference at that altitude, which broke the aircraft into several pieces. Such an issue was well worth investigating further; so much so that BOAC donated one of its remaining Comets to be used as a testing airframe to perform experiments on.
This was done by simulating thousands of pressurization cycles using a water tank in which the fuselage was placed. The results were conclusive: metal fatigue due to repeated pressurization and de-pressurization of the airframe had caused cracks to appear prematurely in the metal skin of the fuselage, which eventually failed.
However, a common misconception is that the square windows fitted in the aircraft were to blame. In fact, the accident at Elba was determined to have been caused by an initial crack that formed on the top side of the aircraft fuselage. A square window would indeed experience high stress at the corners; however, this was a well-known fact at the time. For this reason, the designers of the Comet had not made the windows of the aircraft completely rectangular. The corners were not sharp, but featured an angled edge to distribute the stress more evenly, although investigations concluded the stress in the skin around these areas was still much higher than in other areas. While it is true that this window design was still weak and thus contributed to the two fatal crashes, the source of the cracks was another.

To improve the aerodynamics and efficiency of the aircraft as a whole, engineers wanted the smoothest possible fuselage surface. In earlier aircraft, the rivets connecting the skin to the frames and stringers on the inside of the structure protruded from the surface of the fuselage, creating extra drag. On other aircraft, this had been overcome by machining a hole into the skin of the fuselage for the rivet head to sit in. However, advances in aluminum alloys meant a thinner skin could be used on the Comet, providing the same strength but with a lower weight. The downside of this was that the skin was too thin to drill a suitable hole in.
As a solution, designers decided instead to use the ‘punch rivet’ technique, where rivets are applied with enough force to dent into the skin, creating a flatter surface. In doing so, though, the rivets created uneven holes and microfractures in the skin of the aircraft, which, combined with the fact that no glue or sealant was used in combination with the rivets, facilitated the propagation of cracks and metal fatigue.
Unfortunately, this was only discovered after a second crash. In April 1954, just 3 months after the first crash, a second Comet came down off the coast of Naples, Italy. While the wreckage was not fully recovered to confirm the cause of the crash, a similar sequence of events probably occurred in this case.
Following this second deadly accident, the Comet was grounded and its airworthiness certificate revoked. When the investigation findings were published, all Comet 1’s were retired, with de Havilland working quickly to develop a second variant, the Comet 2, which featured a thicker skin and elliptic windows. By that time though, the jet age was in full swing, with de Havilland facing stiff competition from the United States, comprising of the Boeing 707 and Douglas DC-8. Both of these aircraft became much more popular than the Comet, of which only 114 were built.
Comments (2)
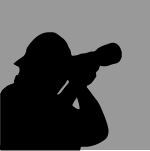
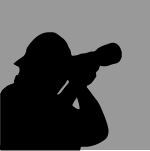
Add Your Comment
SHARE
TAGS
INFORMATIONAL De Havilland Comet Aviation History Aviation HistoryRECENTLY PUBLISHED
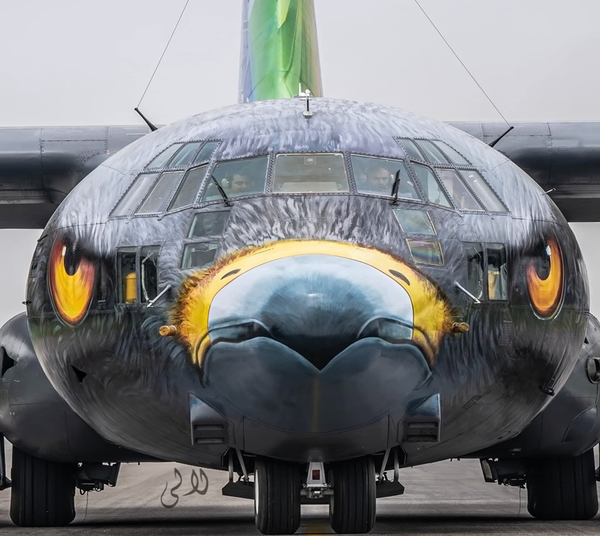
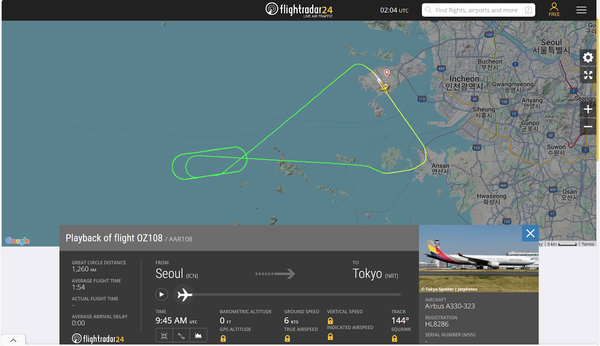
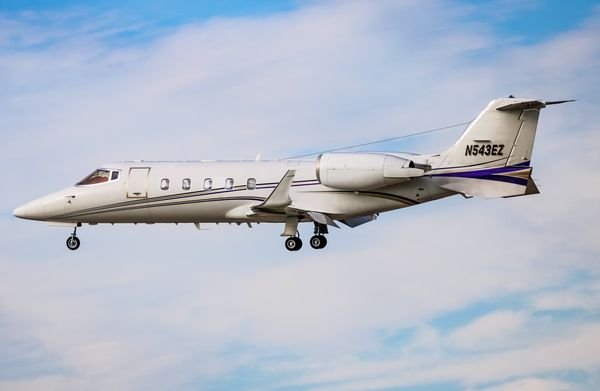