3D printing technology has come a long way since it was established in 1986. Currently, it is possible to apply 3D printing in all walks of life, from minute toy chairs to fully-printed houses. Its applications are widespread from artwork to architecture.
The aviation industry constantly searches for innovative and cost-effective solutions that break boundaries and push new frontiers. Considering the production of some aircraft pieces, it may be more cost-efficient to use 3D printing for smaller parts of the airplane. 3D printing reduces production time and can create complex structures that are difficult to manufacture by hand.
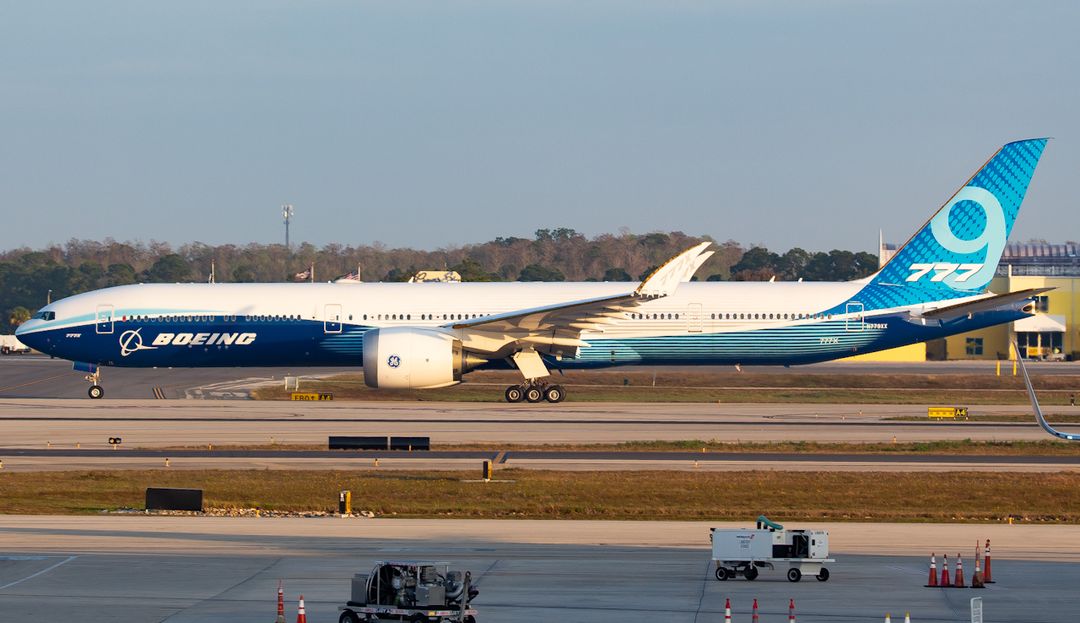
Aircraft manufacturers like Boeing and Airbus commonly use traditional methods such as machining, molding, and casting. While utilizing these methods, excess parts can occur which are cut off during the manufacturing process. The lack of precision concludes in a time-consuming process and costs more since more material is used than necessary.
Also, these methods are limited when it comes to geometry. In 3D printing, CAD programs assist with creating precise designs where almost no material is lost and the shapes that can be curated are endless.
To grasp the possible use of 3D printing in aviation, it is important to understand the main methods of 3D printing.
3D Printing Methods
As "the inventor of 3D printing," Chuck Hull filed the first patent for stereolithography, SLA, a technique of creating a 3-dimensional object with a computer-controlled moving laser beam constructing the object layer-by-layer. He created and commercialized both SLA and the .stl format, the most common forms of 3D printing.
FDM: Fused Deposition Modeling
This method extrudes a thermoplastic filament through a heated nozzle. The object solidifies while it cools down. It is known for affordability and versatility and is widely used among hobbyists and professionals.
SLA: Stereolithography
This method utilizes a build platform submerged in a liquid resin. After the process, it is cured layer-by-layer with a UV laser or alternative light sources. The primary benefit of this method is its precision. Therefore it is commonly utilized in jewelry making and dentistry.
SLS: Selective Laser Sintering
This method uses a high-powered laser that fuses powdered materials to construct solid objects. It is compatible with metals, plastics, and ceramics. SLS can be used for industries such as automotive and aerospace since they require durable parts.
The Future with 3D Printing
Given the evolution of technology and the vast range of benefits of 3D printing, it is inevitable that some aircraft manufacturers will shift to incorporate 3D printing. Manufacturers prefer low-cost, efficient methods with design freedom.
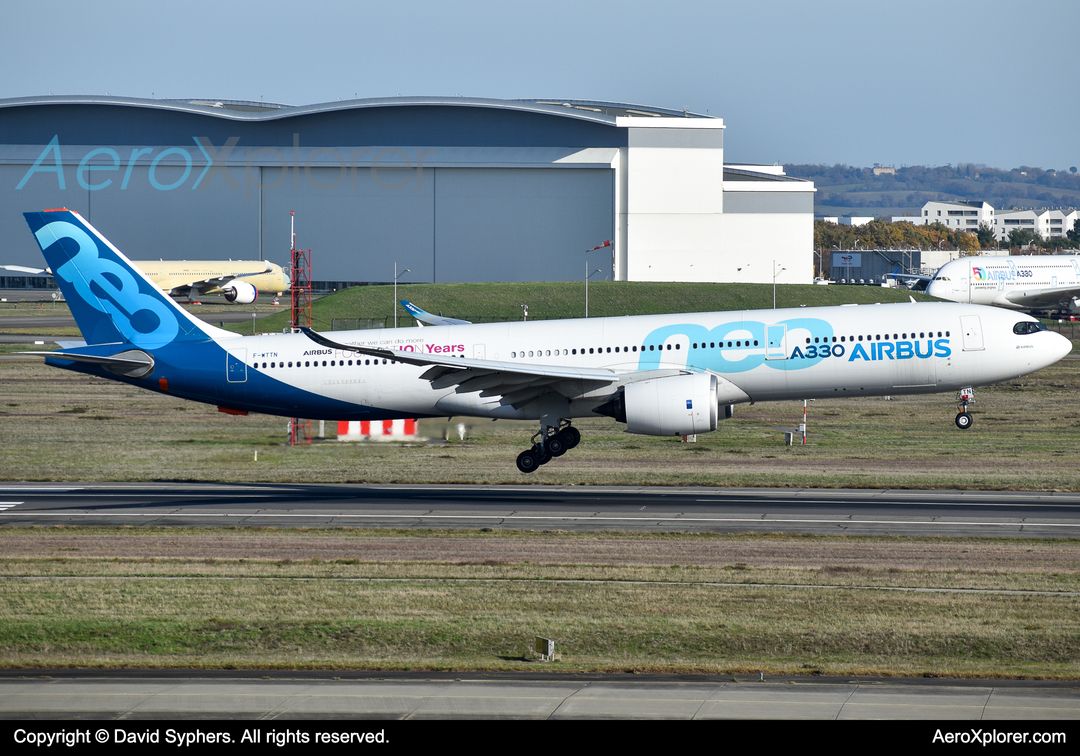
This crucial technology can reduce inventory and eliminate expensive molds, jigs, and fixtures. The parts for the aircraft can be produced on demand. During the printing process, it is possible to multitask the parts to be produced. The procedure eliminates a portion of the assembly process, reducing labor costs.
With high-speed production and precision, it is possible to satisfy the market's demands faster than traditional manufacturing methods. Cost efficiency is a cornerstone of 3D printing's benefits since Boeing stated that it saves around $3 million per plane when utilizing 3D printed elements.
Currently, 3D printing is limited to prototyping and manufacturing less essential parts. However, the technology is evolving rapidly and it is possible to observe some important pieces of the aircraft to be manufactured in the future by the use of 3D printing. It can also assist with the supply chain for Urban Air Mobility (UAM).
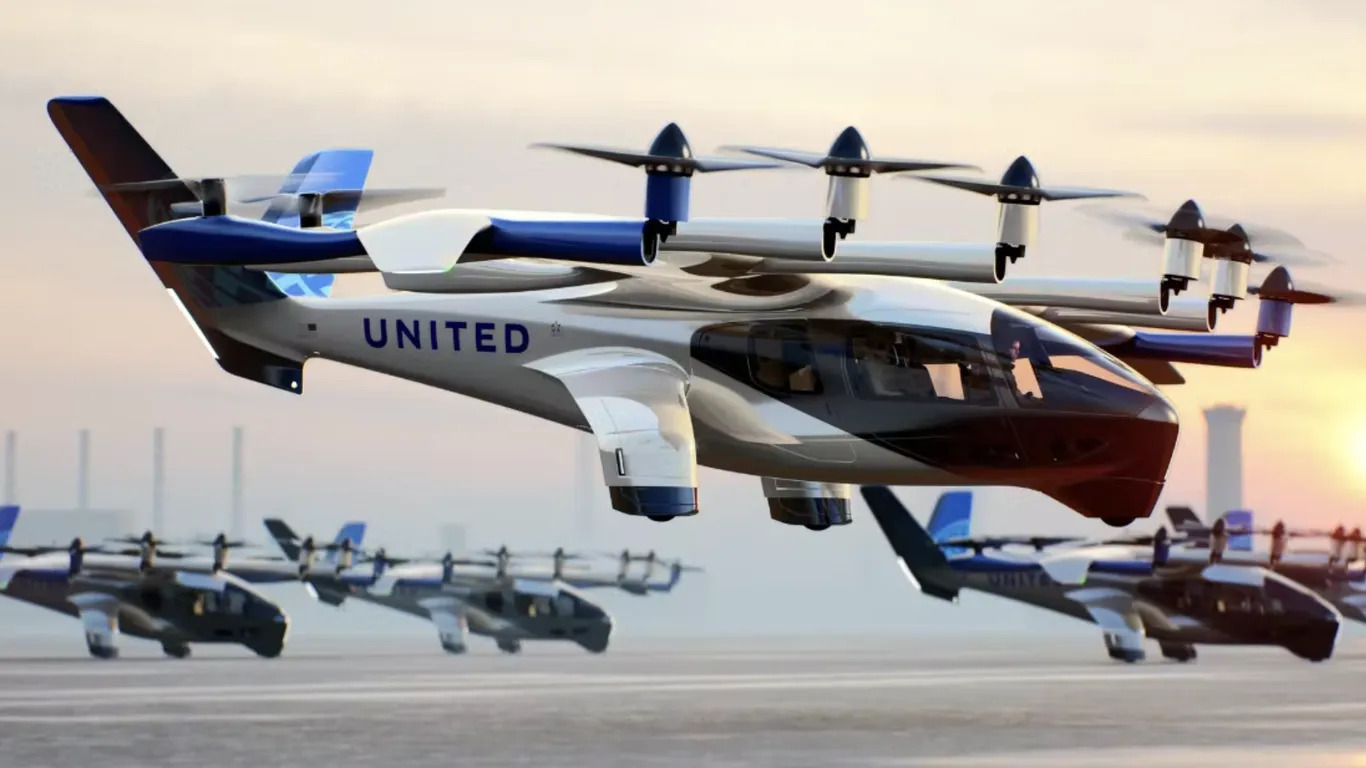
UAM is the concept of air taxis, headed by manufacturers like Archer Aviation and Wisk (backed by Boeing) with orders from airlines like United. 3D printing could assist the manufacture of key parts in air taxis, since parts will be smaller due to the aircraft's small size.
Developers of VTOLs are currently working on 3D printed parts for these aircraft. A new VTOL aircraft prototype from Horizon Aircraft got airborne with nearly 800 3D printed parts.
The Possible Issues
It is a challenge to ensure the quality control and standardization of the 3D printed parts, especially in an industry where safety is imperative. Traditional methods have set manufacturing methods and well-structured quality control processes.
Since the technology itself is relatively new, regulations are constantly fluctuating. Constant testing should be done in order to establish trust in the system. The parts should meet the safety requirements and required performance. There are still fire resistance and long-term durability concerns about the 3D printed parts.
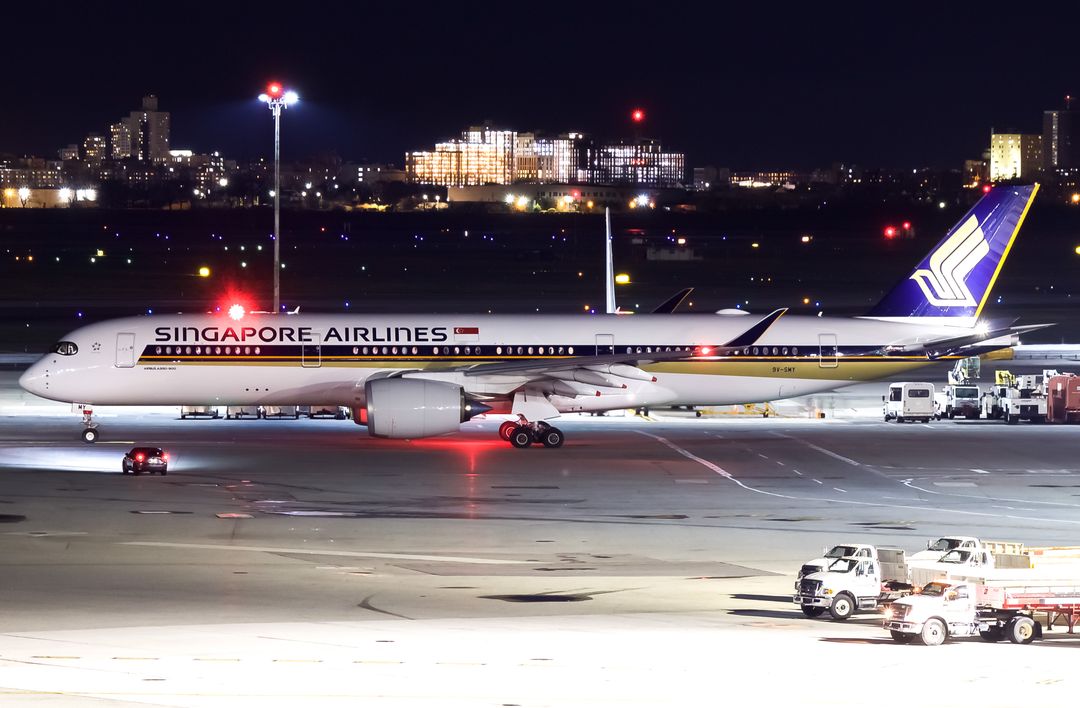
It is possible to achieve good results. Singapore Airlines partnered with Stratasys to create customized cabin parts. These elements were lightweight and flame-retardant at the same time, therefore, creating results in which the parts are compatible with industry standards.
However, it is important to continue tests since the failure process will allow for more safe iterations. Airbus attempted to manufacture titanium brackets for its A350 XWB aircraft, but the complexity of the brackets and the limitations of 3D printing caused significant amounts of rejected parts.
Research and trials are always important for new technologies. Before applying, this process will help manufacturers understand the capabilities of the procedure. The 3D printing for aviation brings many advantages however it will take time to apply it safely like any other new development.
Comments (0)
Add Your Comment
SHARE
TAGS
INFORMATIONAL 3D printingEVTOLVTOLAirbusBoingBoeingAviation TechnologyRECENTLY PUBLISHED
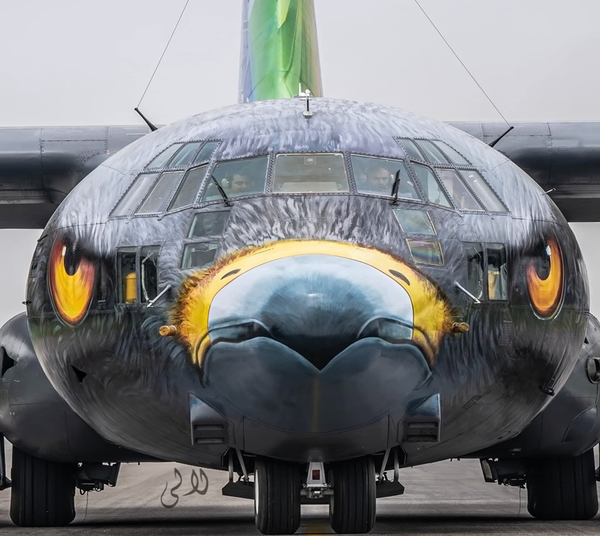
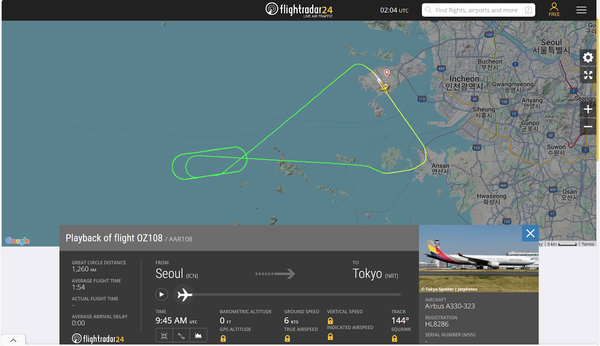
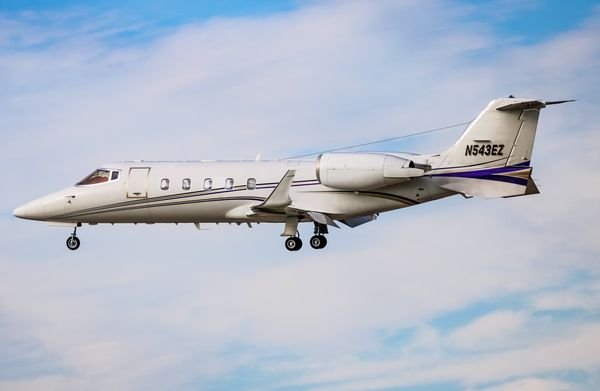